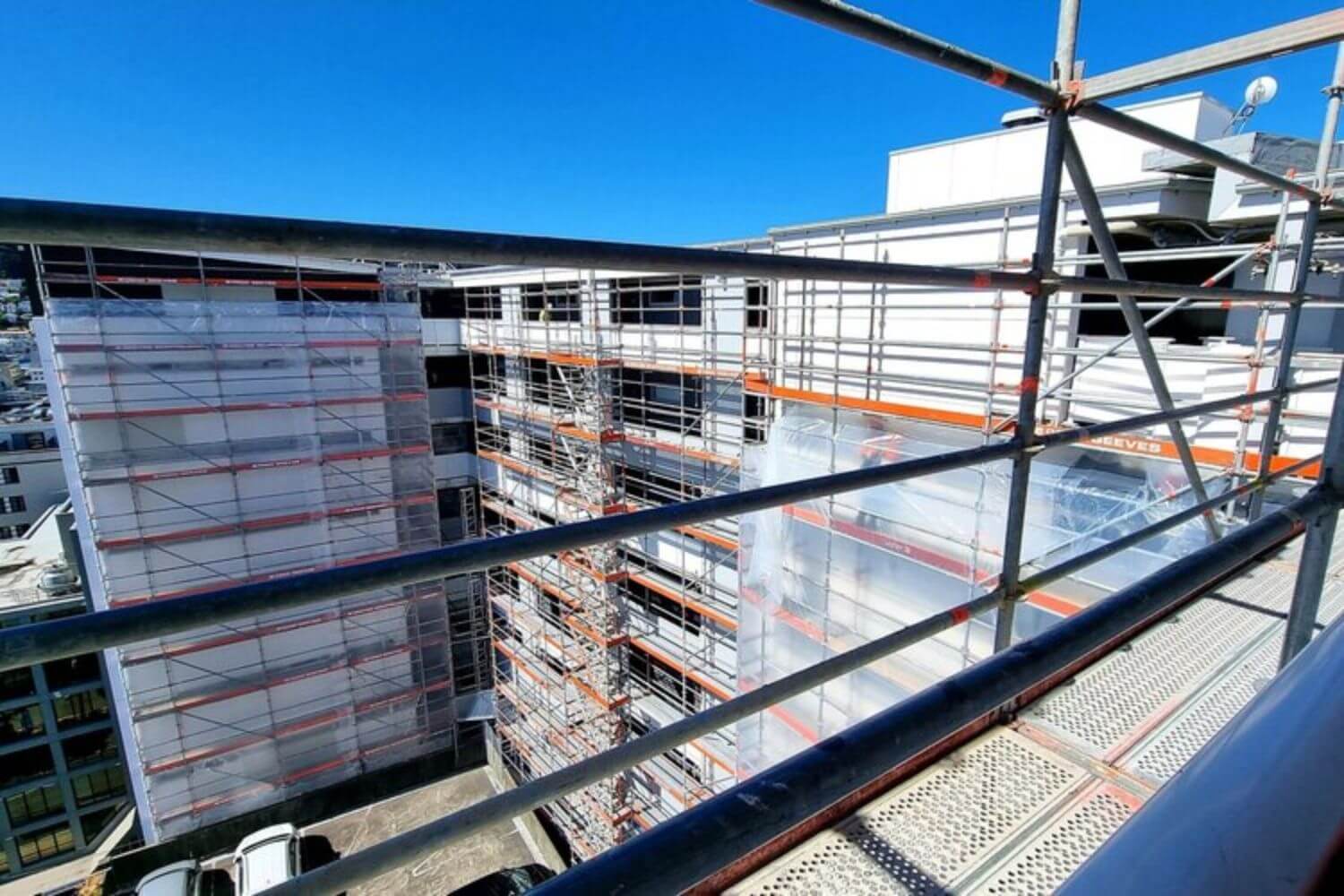
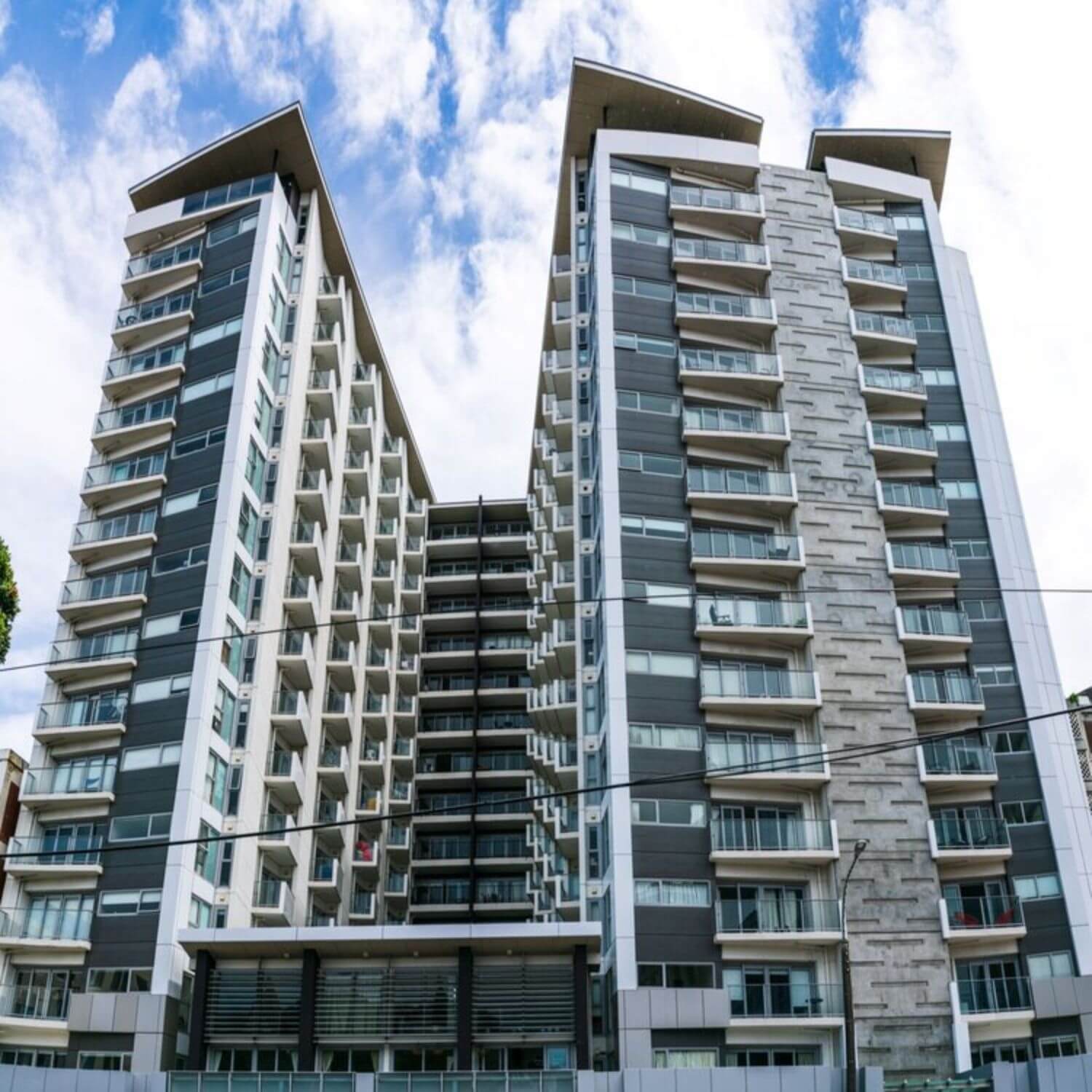
Hawkins was engaged in 2020 to replace 330 front doors and 4050 Breezeway Cladding sheets as Separable Portion 1. Separable Portion 2 was introduced halfway into the build which included 50% external cladding replacement, concrete crack repair and a full repaint of a 15-story building with 930 residents living in the building.
Hawkins provided guidance under the earlier ECI period on buildability issues, assisted with onsite co-ordination and created a culture on site which created a happy site for both workers and residents.
The team spent time fine tuning systems to ensure the narrow open breezeways had adequate space for the building users to operate normally and without being impeded by the construction works. Having the right methodology in place to remove the cladding panels and not to leave excess material lying on the breezeway including screws, nails and dust was vital.
Lessons learnt meetings and conversations with the wider team ensured the right systems were in place to look after the interests of the residents first, but also allowed the correct sequencing to occur.
As construction works evolved, residents had to move their belonging within their apartment every day for 5 days. During this period, the residents space was turned into a tightly controlled construction space.
Front doors and exterior windows were removed, reinstated and fully cleaned within a 7-hour window to allowing residents to use their apartment from 4.30pm.
With a huge amount of plastic shrink wrap being used on this project, a conscious effort was made to find a way to reuse the plastic sheeting. The team found a company in Levin who would take the plastic and turn it into other products. Some of this plastic was used to manufacture a playground slide installed at a local community center in Porirua.
Before works began the team agreed several goals for the project and one ofthe goals was to create a collaborative environment. Collaboration between Hawkins, sub-contractors, client and residents was undertaken throughout the construction programme, with the development of the ‘McDonalds’ installation of doors to how cladding sheets are to be removed.
The complexity of the project required the team to think differently and tested the team’s skill set.
The aim was to create a single approach to the project which could then be relayed out to the wider team.
Agreeing simple goals (eg. Happy Site, Health & Safety Audit ready at all times, Zero Defects) created a collaborative working environment and set a very high standard before the project had started.
Working in a live building with 930 residents was the biggest challenge. This was overcome by slowly changing the residents perceived perception of builders by creating a great culture and attitude on site. Hawkins provided lookahead programmes for communication to ensure the residents are fully informed of the progress. This was measured by the residents Facebook page which began with negative comments around the proposed works to praising the teams for doing a fantastic job in difficult conditions.
The client wanted a stress-free project with minimal complaints from apartment owners. From several comments verbalised at a recent owner’s presentation and emails received it is clear we have exceeded the client’s expectation.